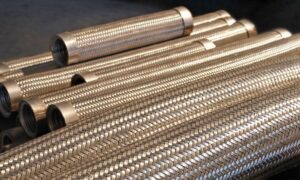
Industrial metal hoses are unsung heroes in many industries. They transport harsh chemicals, abrasive materials, extreme temperatures, and high pressures that would destroy less durable conduits. Yet even the toughest metal hoses are susceptible to corrosion, which can lead to leaks, downtime, and costly replacements.
In this blog, we’ll dive into the causes of industrial metal hose corrosion and outline proven strategies to mitigate the issue, ensuring your industrial operations run smoothly and efficiently.
Why Corrosion Matters
Corrosion is the insidious enemy of metal. It’s a complex electrochemical process that gradually weakens and eats away at metal structures. In industrial hoses, corrosion is often accelerated by factors like:
- Chemical Exposure: Aggressive chemicals, acids, alkalis, and even cleaning solutions can react with the metal, causing degradation and pitting.
- Environmental Factors: Moisture, salt-laden air (think coastal areas), and high temperatures can all exacerbate corrosion processes.
- Galvanic Corrosion: When dissimilar metals in the hose or fittings come into contact, often in the presence of an electrolyte, corrosion is accelerated as one metal sacrifices itself to protect the other.
The consequences of corroded industrial metal hoses are serious. Leaks can cause environmental damage, safety hazards, and product contamination. Unexpected hose failures lead to production downtime and revenue losses.
Prevention is Key: Strategies to Protect Industrial Metal Hoses
The good news is that corrosion prevention is attainable with proactive planning and the right measures. Here’s how to safeguard your metal hoses:
- Alloy Selection: Choose the appropriate metal alloy for your specific application. Stainless steel (especially grades 316L and 321) is a popular choice for its general corrosion resistance. For extremely harsh environments, consider more specialized alloys like Hastelloy or Monel.
- Protective Coatings & Linings: Applying internal linings like PTFE (Teflon) or external coatings like PVC creates a barrier between the metal and corrosive agents. This adds another layer of defense.
- Proper Installation: Avoid over-bending, twisting, or placing undue stress on hoses during installation. Improper installation creates points of weakness where corrosion can initiate.
- Regular Inspections & Maintenance: Implement a visual inspection schedule to catch signs of corrosion early. Look for discoloration, pitting, or any external damage. Internal inspections may also be necessary depending on the materials conveyed.
- Cleaning and Flushing: Periodically flush hoses with appropriate cleaning agents to remove corrosive residues or buildup. This is especially important after transporting aggressive chemicals.
- Cathodic Protection: This technique uses sacrificial anodes for impressed current systems to protect the metal hose by making it the cathode in an electrochemical cell. It’s often used in extremely aggressive environments.
- Monitor the Environment: Control humidity levels where possible and minimize exposure to corrosive fumes or other harsh environmental factors.
Additional Considerations
- Wall Thickness: For situations where corrosion is a major concern, opting for a thicker-walled hose provides greater longevity.
- Hose Design: Proper configuration, including the selection of fittings and end connections, is crucial to prevent crevices and stagnant areas where corrosive agents can become trapped.
Industrial Metal Hoses from J.W. Roberts
You can significantly extend the lifespan of your industrial metal hoses, saving money, and avoiding production disruptions by taking the steps listed above.
When it comes to industrial hoses, trust our team at J.W. Roberts to find the best industrial hoses for your applications. Contact us today to learn about our types of industrial hoses and hose accessories.