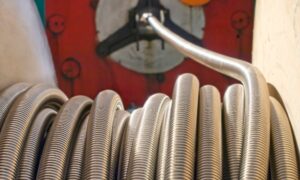
Industrial metal hoses play a vital role in various industrial sectors, providing flexible conduits for conveying fluids, gasses, and even solids. Among the diverse types available, corrugated and strip-wound metal hoses stand out as two popular choices. Each boasts unique features that cater to specific needs, making the selection process crucial for optimal performance and longevity.
This comprehensive comparison will delve into the intricacies of both types, aiding you in making an informed decision for your industrial application. For precise insights and quick orders, contact our team at J.W. Roberts today!
Corrugated Metal Hoses: Strength and Resilience
Corrugated metal hoses are instantly recognizable due to their parallel ridges, a design that confers exceptional strength and durability. These hoses are typically manufactured from stainless steel or other corrosion-resistant alloys, making them impervious to harsh chemicals, high temperatures, and extreme pressures. Industries like oil and gas, chemical processing, and power generation rely on corrugated hoses for their reliability in demanding environments.
The corrugated structure provides excellent flexibility, allowing the hose to bend and absorb vibrations without compromising its integrity. This makes them ideal for dynamic applications where movement and stress are anticipated. Additionally, their continuous metal construction ensures superior leak tightness, a critical factor in preventing hazardous spills or loss of valuable materials.
However, corrugated hoses do have some drawbacks. Their robust build makes them slightly less flexible than strip-wound hoses, potentially limiting their use in applications requiring intricate bends. Furthermore, their complex construction and premium materials contribute to a higher price point compared to strip-wound alternatives.
Strip-Wound Metal Hoses: Flexibility and Affordability
Strip-wound metal hoses, crafted by winding interlocking strips of metal (usually stainless steel) around a flexible core, offer a unique set of advantages. Their construction imparts an unparalleled degree of flexibility, enabling them to navigate tight spaces and complex routing with ease. This flexibility, coupled with their lower cost, makes them a preferred choice for applications where maneuverability and budget constraints are primary concerns.
While their flexibility is impressive, strip-wound hoses do have limitations. Their lower pressure and temperature resistance make them unsuitable for extreme conditions often encountered in heavy industrial settings. Additionally, the interlocking design, while contributing to flexibility, can be more prone to leaks compared to the continuous construction of corrugated hoses.
Choosing the Right Industrial Metal Hose
The decision between corrugated and strip-wound metal hoses ultimately hinges on the specific demands of your application. Factors such as pressure, temperature, required flexibility, leak tightness, and budget must be carefully considered.
If your application involves high pressures, extreme temperatures, or the conveyance of hazardous materials, a corrugated hose is the clear choice. Its robust construction and leak-tight design ensure safety and reliability under demanding conditions. However, if flexibility is paramount and the application’s operating conditions are less extreme, a strip-wound hose can offer a cost-effective and adaptable solution.
In conclusion, both corrugated and strip-wound metal hoses have their rightful place in the industrial landscape. By understanding their strengths and weaknesses, you can confidently select the ideal hose to meet your unique needs, ensuring optimal performance, longevity, and safety in your operations. Contact our team at J.W. Roberts to find the right industrial metal hose for your operations.